Secondary Materials and Waste Recycling Commercialization - Raw materials
Source: eKapija
Sunday, 07.08.2011.
15:57


Secondary Materials
Plastic
Supply Chain: A simplified plastic recycling supply chain is shown in the diagram to the right. Readers interested in plastic recycling are referred to Part 2 of this assessment (Profiles & Actors) for more detailed descriptions of the activities and actors. This section will present the supply chain and a comparison of the large processors who generally serve as the ultimate buyers of the materials. The supply chain can be said to consist of three basic levels: collection, separation & sorting, and processing.
Collection: There are generally three types of collectors in the plastic sector: individual, organized and private.
Individual collectors include Roma and other small collectors, and individuals operating on a larger scale organizing collection, often including commercial and industrial waste (Kandic, Kraljevo). Individual collectors can also include citizens or groups that collect waste for an environmental goal.
Organized collectors include communal waste collectors: JKPs, strategic waste management partners in PPPs, and in a few cases private operators (Brdja,Trstenik).
Private collectors, such as those described in the previous section, often serve as both collectors and sorters. These actors are registered businesses and serve to collect, separate and consolidate waste for the ultimate processors or end users.
Separation & Sorting: At present in Serbia there are few examples of strictly sorting operations. A number of actors manage sorting lines (Pima, Brzanplast) but they do so as
part of a larger operation. In fact, virtually all of the processors, both large and small, also manage sorting operations. The Recycling Backyards concept, if implemented, would be an example.
Processing: There are numerous types of plastic processors in Serbia that specialize or utilize recycled plastic. First are the PET processors, larger companies processing from 50 to several hundred tons per month. Next are the large non-PET processors, producing LDPE folio (Brzanplast), hose and piping (Nives), or granulate. Finally are the hundreds of small plastic processors scattered around Serbia producing folio and injection-molded products, most of whom process recycled material to a greater or lesser degree (Nikolo, Vlada-Pak, Interprodukt, Nima).
Supply & Demand: There is an under-supply of secondary plastic materials on the market, evidenced by surplus capacity in most buyers and processors, and competition for materials, including PET. Greentech, Saniplast, Intercord and Deni Komerc all process PET and all have additional capacity and demand. Greentech notes this as a positive, as it creates demand and helps cover times of crisis, such as when during the peak of the economic crisis Greentech was the processor buying PET. To illustrate the scale, Greentech collects 300 tons/month of PET in Serbia; in their two Romanian plants (producing mainly Polyester Staple Fiber) they process 5000 tons/month. Development efforts should focus on increasing collection by expanding existing operations and facilitating the startup of new initiatives.
Plastic Processor Summary: Most, perhaps all, of the largest plastic processors, including all major PET processors, were interviewed in this assessment. Annex 4 provides a summary of each processor interviewed, including materials and quantities, collection methods and outreach, and the company’s production. The reader is also referred to Part 2 of this assessment for a detailed description of each.
Paper
Supply Chain: Paper, especially cardboard, is recycled fairly efficiently in Serbia. It has value and is collected in varying levels of in probably every city, small town and many villages in Serbia. The paper recycling supply chain is presented in the diagram, with key actors interviewed noted in the boxes. Each actor is profiled in detail in Part 2 of this assessment.
The supply chain consists of collection, consolidation, and processing.
Collection: Paper is collected in three ways:
Individual collectors (Roma and others) collecting cardboard directly from containers and small retail shops.
Organized collectors (JKPs and strategic waste management partners) and some slightly larger private operators like Kandic and Urvis.
Commercial and industrial sources of waste paper (cardboard packaging and print shop waste) sell their waste to consolidators who pick up the waste from the source. These arrangements are typically structured so that a single operator is required to take all of the waste, and pays the source for the waste, either by a fee or by weight (presumably they do not take communal waste generated by workers). In the case of supermarkets, the consolidator typically owns the containers. Pickups are usually arranged on demand.
Consolidation: Consolidators can be placed into three categories based on size:
Small consolidators, who purchase primarily or solely from individual collectors; in urban centers, these actors are often Roma. Most small towns and villages in Serbia also typically have a buyer of paper, metal and other materials; such consolidators might buy from 10-100 tons/month. Small consolidators serve medium consolidators, almost never selling directly to the processors.
Medium consolidators collect from 100-1000 tons/month; several were interviewed and profiled in this assessment. These consolidators are also usually the buyers of JKP-collected cardboard and hold agreements with commercial and industrial waste sources.
Large consolidators, of which there are only a handful in Serbia (Inos and TechnoPaper, neither of which was interviewed) collect more than 1000 tons/month. Medium consolidators will sometimes sell their paper to large consolidators and achieve a better price because of the higher quantities. In these cases, the large consolidators generally does not handle the paper, but simply organizes supplies from different sources and holds the agreement with the buyer. It seems, and is logical, that the large consolidators serve export markets.
Processing: Most of the paper and cardboard production in Serbia is handled by companies in the Kappa Star group (see inset). Together they account for over 9000 tons/month of paper and cardboard production. Besides those companies, there are two remaining paper factories in Serbia: Bozo Tomic in Cacak, and Fopa in Vladicin Han, producing about 1700 tons/month combined. In September 2009, the German Hamburger Group opened a large factory in Hungary with a capacity in excess of 30,000 tons/month. The factory is not yet operating at full capacity but will become a major regional buyer and competitor for waste paper. There is already some waste paper export from Serbia (to Croatia). Meanwhile, Umka imports high quality white paper from other countries in the region.
Policy & Support: Umka and paper consolidators have not received any financial support for recycling from the government, as opposed to EU countries which received subsidies during the economic crisis that provided value to collected paper. A project proposed to the Government to subsidize Roma collection for those who legally registered was not supported. According to Umka, Croatia subsidizes paper collection at €30/ton; Umka supports investing in collection and efficiency improvements and hopes that the new laws will result in effective instruments of support to the Serbian recycling sector. Umka, like most other actors, believes that the current national targets (5% recovery, 4% recycled) are too low, partly due to lobbying efforts by Seko-Pak. They are discussing a future arrangement with Seko-Pak to support investments in JKPs and private collectors to meet national targets. Umka supports the philosophy that the green economy will create jobs.
Glass
Supply Chain: At the outset it should be noted that glass recycling in Serbia is fairly uncommon: demand and prices are low, it is heavy (transport costs are high), and there are few collectors willing to work for the low margins. That said, there are two supply chains of glass recycling in Serbia (see diagram and Part 2 of assessment). Many, probably most, cities in Serbia do not a buyer for glass in either supply chain.
Unbroken Packaging Glass: The first supply chain deals only with unbroken glass bottles and jars of all types and sizes. There is a small network of collectors, often individuals working informally, who buy virtually any unbroken glass container, organize and consolidate types and sizes by trading with one another, and sell or trade the bottles and jars to their network of bottlers and food producers. Kalimero Komerc in Krusevac is the only example of this type of collector interviewed for this assessment, though several others (mostly individuals) were identified in other cities. The average price for a standard glass jar or bottle is 3-5 RSD. Mr. Popovic, the owner of Kalimero Komerc, says that 90% of his sales are to individuals, not companies.
All Packaging Glass: The second supply chain deals with any packaging glass, broken or unbroken. Currently, Srpska Fabrika Reciklaza (SFR) near Aleksinac appears to be the only buyer in Serbia, though a partner collector, Glass Rec, may soon begin working in Belgrade. SFR, a privatized operation employing 13 workers, crushes the glass and sorts it by size, and sometimes by color; they have a capacity of 30,000 tons/year; all of the crushed glass is exported.
Collection details were vague but include some containers in Aleksinac owned by SFR, individual collectors, bottlers, and a number of JKPs and collectors of commercial and industrial waste who are required to collect glass along with other materials (Pima). One JKP informed that SFR pays 0.75 RSD/kg for glass.
Serbian Glass Factory: Srpska Fabrika Stakla (SFS) is the only Serbian producer of glass packaging; SFS is owned by Serbia Gas (63%), Bulgaria Glass Factory Pleven (25%), and company ownership (balance). At this time, SFS only recycles broken glass from its own factory (rejects), clients (damaged), and limited private collectors (clean). From the private collectors, the company is paying 2.0 RSD/kg for white, 1.5 RSD/kg for sorted color, and 1.0 RSD/kg for mixed. They are, however, interested in beginning glass recycling on a larger scale.
Recycling Capacity: After privatization, the company had 10,000 tons of broken glass in storage, plus additional quantities waiting return from clients. In addition, they routinely have quantities of internal glass that gets recycled (broken, reject, surplus). So for some time, the factory has been trying to reduce its inventory of broken glass and now appears ready to undertake more serious collection and recycling. In addition to reducing inventory they have also been making some changes to their process to decrease the amount of rejected and damaged production.
Recycling Economics: SFS stated that they have two interests to begin recycling: firstly because of ecological responsibility, and secondly economics. Simply put, glass is cheaper to melt than quartz so recycling saves energy and reduces the cost of production. Energy is the biggest expense in glass production; for every 10% of recycled glass, a savings of 3% can be realized in energy.
Recycling Requirements: The glass factory is interested in collecting and recycling glass of all colors. In order to be recycled, however, the glass must be totally pure with no inorganic contamination. Some levels of organic dirt and dust are tolerable, but any ceramic, metal, stone or other inorganic substances can damage the furnaces; the factory already has magnetic separators for ferrous metals. Therefore the glass should be cleaned and sorted prior to recycling; this could be done either by the collectors, an intermediary, or the factory itself. An automated cleaning and sorting line requires an investment of approximately €3 million; credit or other financing scheme would also be necessary. There is no existing collection network on which to rely; transport is also an issue as shipping broken glass must be done in different containers than normal shipments.
Glass Demand & Trends: The annual demand for glass in Serbia is between 130-150K tons/year, of which approximately 30% is produced by SFS; the remainder is imported. Despite the global trend toward plastic containers, SFS stated that demand for glass is increasing, particularly for small, non-transparent bottles such as those used for small bottled wines. The company hopes to increase its production to 100K tons/year by 2011 by increasing its share of the Serbian market.
Collection: The glass factory does not have a developed strategy for recycled glass collection, though they do accept returns from some companies (e.g. Knjaz Milos). All glass currently accepted for return is clean and doesn’t pose a contamination hazard. They have had no other contact with collectors and would require a period and/or assistance to develop a collection network.
Metal
Supply Chain: Metals, both ferrous and nonferrous, are recycled quite efficiently in Serbia through a vast network of collectors and buyers covering virtually every city, town and village. Individual collectors, mainly Roma, collect metal from containers and door-to-door; many citizens facilitate the process by placing metal waste alongside, rather than inside, of containers. Industrial and commercial metal waste is recycled even more efficiently. It is likely that every producer of metal scrap has a buyer established, either under a long-term agreement or periodic negotiated sales.
Consolidation: There is a large network of metal buyers across Serbia. In the former MESP recycling database, metal recyclers were by far the most prevalent, with 55 registered metal recyclers; the IFC Recycling Linkages project had 65 in their database. A typical consolidator, Vet Prom in Krusevac, was interviewed in this assessment; Vet Prom collects 150-200 tons/month of metal, mostly from larger firms and factories in and around Krusevac; they have a one-year contract with most generators. Vet Prom accepts all metal, including machines, motors, vehicles, processing equipment and scrap. The equipment is disassembled, sorted and baled on the Vet Prom lot, where it is then sold to various buyers who reprocess the metal or melt it into ingots. Vet Prom also collects LDPE and PP from the same commercial and industrial sources. In the city of Krusevac (city pop. 75,000), there are around five such collectors.
Markets: Most of the steel collected in Serbia is either sold to the US Steel factory in Smederevo or exported, along with other metals. Recan (below) manages a Serbian program collecting aluminum cans. Some other metals are also processed locally: lead by the Farma Kom battery factor in Sombor, copper by Jugo Impex in Nis, and others.
Recan: Recan, a wholly-owned subsidiary of Ball Packaging Europe, operates recycling centers in Serbia where used aluminum cans are sorted, compressed and returned for recycling. The recycling centers cooperate with waste management operators, scrap metal dealers, supermarkets, shopping centers, petrol stations and other businesses, providing a network of collection points to ensure that consumers have a convenient and problem-free facility to return used beverage cans. Recan also provides consulting services related to logistics and quality, quality checks, analyses and documentation, and payment handling. Recan offers attractive prices for used beverage cans that meet Ball’s quality specifications.
Electronic Waste & Batteries
Supply Chains: There are three licensed electronics recyclers in Serbia: Bozic i Sinovi in Pancevo (visited), Eko Metal in Vrdnik and CE Trade in Belgrade. There is only one licensed lead battery recycler in Serbia: Farma Kom (Galenit Cluster, visited), the automotive battery manufacturer in Zajeca near Sombor. Due to the specialized nature (in the case of electronics recycling) and the sole source (in the case of battery recycling) the discussions below are based on information provided in the two interviews (condensed from the profiles in Part 2 of this assessment). Related to electronics recycling it is likely that the three recyclers operate considerably different from one another, so the explanation below applies only to Bozic i Sinovi.
BiS Profile: BiS (Bozic i Sinovi) has two core businesses: IT recycling and software development. They recycle all electronic and electrical equipment and waste, plus magnetic tape and fluorescent bulbs in a 2-floor, 3000 square meter facility in Omoljica, approximately 10 km outside Pancevo. Gowi, the IT/software company, was recently separated from BiS; in 2009 Gowi won an award in 2009 from SIEPA for the largest increase in export business. BiS also serves the Ministry of Trade & Services by destroying pirated CDs and DVDs, recycling all of the plastic from the discs and cases; they provide a similar service for Microsoft. They have also begun providing a service to wipe hard disk data from clients with sensitive data, such as banks.
Collection: BiS collected 330 tons of electronic waste in 2009, a “very low” figure according to the company. Most of the collection (97%) is done directly with businesses (B2B) and government offices; both BiS and companies reach out to one another and BiS cooperates with NGOs. Telenor, Price-Waterhouse-Coopers, and banks in Serbia are key clients. Without organized collection it is difficult to reach citizens and household electronic waste; initiatives, containers and collection infrastructure are necessary. The company has had communications with the strategic waste management providers Brantner and PWW. BiS is currently limited on the supply-side and wants to develop collection and transport services to begin developing citizen collection services all over Serbia.
Galenit Cluster Profile: The Galenit Cluster is comprised of the Serbian battery factory Farma Kom and includes members from battery distributors and retailers, auto services, collectors, two citizens associations, Institute Kirilo Savic and Nis Faculty of Electronics. The cluster manages eight battery storage centers and 150 collection sites (typically retail stores and services). Farma Kom is the founder of the cluster. The Galenit Cluster accepts all batteries: lead-automotive, industrial and general purpose. Lead batteries are recycled in the Zajeca plant and other batteries are currently being accumulated and stored for future processing or export. Galenit is responsible for collecting and recycling 15,000 tons of batteries per year.
Collection: Galenit is confident that they collect 95% of all automotive batteries in Serbia, with only 5% staying somewhere outside the system. They have 3000 special, licensed containers in Serbia: each service has two, with the remainder in public, private, military and transport sites. In August 2009 they were granted approval to begin importing waste batteries; they imported a relatively low volume of 5000-6000 tons but expect the volume to increase since Croatia, Montenegro and Macedonia have no recycling facilities. Farma Kom pays 30 RSD/kg for automotive batteries, a portion of which is used to support the Galenit Cluster. They accept the used mobile phone batteries from the Telenor initiative. They are also storing CRTs for future processing or export since they also contain lead; this is a strategic move as they are preparing for large volumes of CRTs as consumers trade in their old televisions and monitors for LED and plasma screens.
Projects: Galenit is registered as a fund (association of businesses) and implements recycling development projects. In a recently-approved ISC-financed project Gelenit and project partners will help register small collection businesses (mainly Roma) and provide training and initiatives to transition Roma into the formal sector through banking, registration and health services. Cluster development was supported by the Ministry of Economy and Netherlands Government. They also were awarded an EC cross-border project with Romania, and regularly conduct battery collection campaigns through NGOs and schools. They noted that all battery recycling project proposals should have their participation and consent since they are the only recycler.
Wood
Supply Chain: There are different wood and waste wood supply chains in Serbia based on origin and type of wood, products and materials produced, and form of waste wood. In this assessment, three woodworking businesses and one wood waste collector were interviewed. Woodworking businesses typically use a portion of their waste to operate drying ovens for their incoming supply; despite that, they have a surplus of bark and trimmings, cut waste, chip and dust. The three woodworking businesses are all located in south-central Serbia and all had received donations (50-50 cost share) of sawdust briquette machines.
Wood Waste Disposal: There are many saw mills and wood processors in the region and many of them simply throw their waste into rivers. Some companies report that there are transporters who deliver wood to processors and take some of the waste when they are able, presumably for briquette or pellet production. Some mills were observed on the road with large canvas bags of waste placed along the road apparently waiting to be picked up.
Marinkovic Mill, Raska: Marinkovic is a third-generation family business and produces a range of wood products including prefabricated wooden houses, furniture, custom kitchens, doors and windows, and other wood products. Marinkovic processes raw timber and has substantial quantities of bark and trimmings from rough cutting (2.5 tons/day); they also do a lot of shaping, which generates a large quantity of chip and dust (10 cubic meters of sawdust per day), creating a disposal problem. At times, they have a buyer who will accept up to five tons every two days, but it is intermittent; the wood is sold for a minimal fee but it solves a short-term disposal problem. The company would like to invest €10-€30,000 in new drying equipment and a new briquette machine, but is not currently positioned for capital investments due to decreased production and outstanding credit obligations. Due to the economic crisis, the company’s production has decreased from 11,000 cubic meters in 2007 to less than 3000 cubic meters in 2009.
Grozd, Ivanjica The main production of Grozd concerns gluing together small boards and strips into larger boards for further processing by himself and others. In addition to edgewise gluing, he also has the latest technology for end-to-end gluing. The company has modern, computerized equipment and is a very clean operation. Grozd uses a portion of their wood waste for fuel for drying, and produces briquettes from the remainder, selling them for €120/ton, including some export. The current briquette machine (donated in part by USAID) is undersized for Grozd, at 140 kg/hr; Grozd requires 250 kg/hr to process all of their waste, requiring an investment of €40-45,000.
Brest Parket, Ivanjica: Brest originally began producing wood windows and doors, and subsequently moved into parquet which is now their main product. Brest processes 40-50 cubic meters of wood per month and manages a shop located near the factory. The company employs ten workers and wishes to remain roughly the same size. In 2009 the company was processing only 50% of its 2008 levels due to the global economic crisis. Brest received a co-financed donation of an 80 kg/hr briquette machine from USAID but is not currently using it because of complaints from neighbors about dust when preparing the waste for briquettes. The company hopes to move to another location in 2010, where they hope to be free from what appears to be frequent complaints from neighbors. Once they move they plan to process 100% of their waste. At present they use a small amount of their waste for their dryer and give the remainder to an unspecified individual who recently began producing pellets. The company has 2 tons/month of surplus waste that can be processed into briquettes or pellets. If they move to their new location, they may be interested in taking waste from others but not on a large scale.
Dorado, Kragujevac: Dorado company has two main activities: i) producing sawdust heating briquettes from wood waste (50 ton/month); and ii) collecting and baling paper (150 ton/month, mostly cardboard) and LDPE (10 ton/month). The owner, Mr. Dejan Radovanovic is a young, energetic entrepreneur who enjoys the collection business. Dorado started in collection, then moved into wood waste about a year later after receiving an offer from Forma Ideal, located several hundred meters from his facility. At the time Forma Ideal was disposing of their sawdust in the landfill so he saw an opportunity to use the waste to produce briquettes. He originally was allowed to take the sawdust for free but then the Holcim cement factory offered to buy the wood waste so he was then forced to begin buying. He currently pays about €10/ton for waste and sells briquettes for €80-90/ton.
Construction Waste
Construction Waste Interviews: Two companies were interviewed with respect to construction waste: Susa, a large company specializing in demolition, site clearance and remediation, landfill closure and remediation, hydro-technical works, and oversized and heavy equipment transportation. Susa demolished a Lafarge cement production plant (see inset), the Hotel Yugoslavia, and numerous other large structures. Most of the demolition work is done with modern mechanized demolition equipment, though some particular structures, such as the chimneys of the Lafarge plant, were demolished with explosives. Stevanovic Invest is one of the largest construction companies in southern Serbia, and they have projects throughout Serbia. Stevanovic Invest employs 230 workers.
Construction Material Salvaging: According to Mr. Stevanovic, few materials are salvaged from demolished buildings, homes and other structures by construction companies. Many construction materials are reused but it appears to be the responsibility of the owner to do so. In actuality, if nothing else workers would probably organize salvaging rather than simply sending to the landfill. The company’s involvement is limited to selling metal to collectors, and at times reusing a “very small percentage” of roof tiles. There is rumor of some stores dealing with second-hand construction materials imported from Germany, but none were identified.
Concrete Recycling: Construction waste is the second-largest waste stream behind municipal solid waste; according to estimates concrete and by-product waste consumes 17% of worldwide landfill space. Most countries do not have a concerted solution for its management and disposal, in part due to efforts on the part of construction companies to prevent mandatory recycling. Concrete recycling is, however, gradually becoming more common due to improved environmental awareness, governmental laws, and economic benefits. Concrete is recycled by separating the softer materials and then passing it through a crushing machine, often along with asphalt, bricks, and rocks. Rebar and metallic reinforcements are removed with magnets and recycled through traditional metal recycling supply chains. The remaining aggregate chunks are sorted by size, with larger chunks sometimes being reprocessed. The resulting pieces are reused as aggregate base gravel, with fresh concrete or asphalt placed over it. Crushed recycled concrete can sometimes be used as the dry aggregate for new concrete if it is free of contaminants, though this affects the strength and properties of the concrete and is therefore prohibited in many jurisdictions.
Susa Demolition: In the case of the Lafarge factory, Susa recycled or disposed of 30,000 cubic meters of waste in a process similar to that just described. The resulting chunks of concrete were either used as aggregate on Susa construction sites or sold as a gravel substitute. Steel was sold to metal recyclers. The crushed concrete and bricks are sold for a price up to 50% less than that for standard gravel:
0-30 mm: €9/square meter
31-60 mm: €8/square meter
61-80 mm: €7.5/square meter
>80 mm: €7/square meter
Initiatives: Susa recently purchased a 2 ha site where they wish to build a recycling yard. The company recognizes the need for recycling on large-scale demolition projects, both for the economic benefit and for reducing unnecessary demands on landfill and other disposal methods. Susa wants to position itself as a leader in demolition and construction waste recycling. Stevanovic Invest is interested in two segments of construction waste recycling. The first is traditional crushing and pulverizing of demolished concrete; the separated metal is sold to US Steel and the concrete is crushed to 30mm and used as a gravel substitute. The second is concerned with recycling excess concrete and wash water from concrete mixing and equipment/vehicle washing; the system collects the water, cement and aggregate in pools and reuses it in the production of new concrete. The necessary investments are €250,000 and €100,000, respectively. The motivation for the investments is to be positioned to more successfully compete on large demolition projects.
Cement Industry & Tires
Cement Production in Serbia: There are three cement plants in Serbia with a total production of around 2.7 million tons of clinker per year. (Clinker is the solid material produced by the cement kiln stage that has sintered into lumps of diameter 3-25 mm. Clinker is ground, usually with addition of gypsum, to become Portland cement. It may also be combined with other active ingredients or chemical admixtures to produce other cements.) The three cement plants, their capacity, and alternative fuels permitted and applied are summarized in the table.
Co-Processing Advantages: Co-processing waste in cement kilns has a number of advantages. With regard to cement quality, studies have shown that the bottom ash produced by the waste incineration is trapped in the cement, and no further leaching taking place in the cement and concrete. Gas emissions are also unaffected due to the high treatment temperatures. In comparing with traditional waste incineration, the cement industry burns the waste at 2000 degrees C at a retention time of 15 minutes, versus incineration which operate at 1000 degrees C with a retention time of 15 seconds. Advantages of co-processing waste in cement kilns include:
1. substitute fossil fuels with alternative fuels, thereby conserving fossil fuels;
2. reduce fuel costs;
3. decrease CO2 emissions;
4. does not affect or produce other waste or ash (as is the case with incineration);
5. fast and clean treatment waste;
6. supports the country’s waste management and principle of “zero waste.”
Waste Co-Processing: Cement factories are limited in co-processing quantities, either by regulations and permits, or ideally by the cement kiln and process. Holcim and Lafarge are currently only permitted to co-process tires; in 2009 the quantity was unlimited but beginning in 2010 the cement industry will be limited to only 30% of the total waste tire supply in Serbia. Ecorec is in the application process to begin co-processing Solid Recovery Fuels (SRF); Lafarge has applied to process used oils, shredded solid waste, and animal meat and bone meal. The data and notes related to co-processing and alternative fuels are summarized in the accompanying diagram.
Serbia Waste & Co-Processing Volumes: The co-processing limit of Holcim and Lafarge together in Serbia, all things considered, is 120,000-150,000 tons/year. This compares to 2.2-2.5 million tons/year of total waste generated in Serbia (according to Novi Sad University estimates). Co-processing in Serbia is currently limited by law and the vintage of the kilns; Ecorec would be satisfied for the cement industry to achieve 35-40% TSR by 2013.
Regional Solutions: With respect to municipal and industrial waste (solid shredded waste) the cement industry offers regional, rather than national, solutions. Given the relatively low caloric value of the waste and high costs for transporting the waste long distances, the cement industry is only interested in co-processing the waste on a regional basis with a specific transport radius. Some special industrial wastes with higher caloric value and more uniform composition may be cost effective for national or longer-distance collection.
Wood Pellets & Waste: Given the USAID Serbia Competitiveness Project’s current work with wood pellets, the question was raised as to whether the cement industry would be interested in using wood pellets as an alternative fuel. With wood pellets producing a caloric value of 18 GJ/ton and a cost of €150/ton, the cement industry would not be interested in substituting them as a fuel given that they can pay roughly half this price for coal with double the caloric value. They are, however, looking for sources of “treated” wood waste, such as furniture or saw dust contaminated with oil, or other sources of wood waste which can be collected at a much lower cost to the factory.
Incineration: According to Ecorec, cement is just part of the solution for MSW; incineration is also necessary for large cities (e.g. Belgrade, Novi Sad). Incineration faces obstacles, including €500-600 million investment for a medium-size facility, difficult permitting process, and potential opposition from local communities. EPS has had a business plan for incineration for five years but Ecorec is not optimistic that they will obtain the €1.0-1.2 billion necessary for construction. A small incinerator is planned in Uzice near the Duboko landfill, and is expected to be operational in 3-5 years.
Waste Tire Collection: One certified collector and registered tire recycler, Auto Mirko in Prokuplje, was interviewed. Auto Mirko is the contracted supplier for Ecorec (Holcim) covering southern Serbia. Auto Mirko collects 5-12 tons of used tires per week from “vulkanizers” and auto repair shops; from this collection he uses some tires to produce retreads (his main business) and transports the remainder to Holcim. He typically organizes one shipment per week, traveling to one city or region and picking up all of the tires available. Mirko picks up tires free of charge; in the past, tire companies paid €30/tire for disposal, but when the cement companies obtained permits to co-process tires the tire and auto shops could then transfer the tires to the cement factories and not pay a collector. Mirko transports the tires to Holcim, who covers his fuel cost. In exchange, he is also able to sort through the tires at Holcim and take some for retreads.
Waste Oil
Supply Chains: One waste oil collector was interviewed for this assessment, Bio King in Popovac, near Nis. Bio King is reportedly the only licensed waste cooking oil collector for biodiesel in southern Serbia. The company presently operates under two agreements – one for collection and one for distribution.
Collection: Bio King has an agreement with Bio Oil Austria to supply used cooking oil from southern Serbia; Bio Oil buys the oil for €0.30/L and also loaned Bio King a small collection truck and some startup assistance. Bio King plans to expand collection to cover roughly the southern third or half of the country. The main suppliers are student centers, hospitals, catering companies and big bakeries. He also collects from OMV, and smaller amounts from restaurants and hotels. According to Mr. Mikan Nesic, Serbian law requires generators to give used oil to licensed collectors free-of-charge; therefore, Bio King does not pay for the used oil. Most generators simply dispose of the oil, but there are some unregistered collectors with home-based processes who will pay for the oil (12-15RSD/L), creating illegal competition for Bio King. Oil is collected in 30 and 60L containers provided by Bio King; they are collected on demand. Bio King filters the oil before sending to Austria.
Distribution: Bio King had originally bought some waste oil processing equipment, but subsequently transferred it to an unspecified company in Subotica, who operates the equipment, along with their own, and returns a portion of the biodiesel to Bioking for distribution. Bio King is working with the municipality of Nis to supply biodiesel at a level of 2 tons/month for JKP Nis vehicles to use on a trial basis; the biodiesel will be blended with regular diesel; the partners are seeking financial assistance to install a 3-4 ton tank and pump. The total demand for city vehicles is 4 ton/month. There are also some discussions with Nis municipality to provide collection space for Bio King in return for biodiesel.
Regulatory Environment: According to Mr. Nesic under EU law, countries must add biodiesel to all diesel sold on the market (10%); Serbia does not have this requirement, providing little incentive for biodiesel. Mr. Nesic is optimistic that Minister Dulic will improve the situation, both in terms of supporting production and administrative processes.
Organic (Compost)
Overview: Composting offers a low-cost, economically sustainable treatment for a large volume of communal waste. Composting is simple and fast, with easily-implementable solutions. In addition, the process produces a high quality product with an established market. This section provides a brief overview of composting solutions, based on the presentation, “Composting Strategies for Serbia,” made at the 2009 ISWA Beacon Conference in Novi Sad.
Morphological Waste Composition: According to studies of waste composition in Serbia, 50% of the communal waste currently disposed of in Serbia is organic and bio-decomposable; if we remove certain non-compostable components, we are still left with a waste stream that consists of 30-40% of waste that could readily be treated by composting; sewage waste can also be used in composting operations.
Solutions: Composting solutions for cities and populations require three strategies based on the point of generation: urban, rural and home.
Urban: Urban composting solutions require a collection system. Door-to-door collection is the most labor intensive but produces a purity of 97-99%. Roadside collection is much less costly but produces a product of lower purity, on the order of 85-96%. For Serbia, the author of the presentation at the ISWA conference recommends door-to-door collection with small biodegradable bags and small collection vehicles. Urban solutions also require capital investments in composting plants, some of which (€10-12/ton) can be financed through the Clean Development Mechanism (CDM) of the Kyoto Protocol (see inset). Gate fees cost €20-25/ton, which are competitive in comparison with landfill fees.
Rural: Rural composting solutions require minimal investment and are decentralized, relying on responsible local citizens to manage. In general, a village operation is managed by one or more local citizens who oversee collection and management of the composting operations, encouraging citizen participation. An example of a 2000 ton/year operation in
Austria required 5000 square meter plot and building and an investment of €150,000.
Home: While home composting is not suitable for many population groups, such as those residing in cities, in cases where it is possible, it is the most cost-effective solution. Home composting requires zero investment and no transport and collection systems and costs. Typical home or backyard composting operations can treat 0.6-1.0 tons of waste per year. An example presented was done with 2,000 families and was spearheaded by the local mayor who managed his own backyard compost operation. The community ultimately showed a large commitment and unity, and also participated in a very successful source separation recycling program. Implementing home composting programs require considerable effort on education, monitoring and awareness-raising, and need to develop alternative solutions for households that are not interested in composting.
Legal Framework for Waste Management
Summary: The overview of national and EU policy below is summarized from the Serbia National Waste Management Strategy 2009-2018 (Reviewed Version of June 20, 2009) and discussions with MESP staff. For more detailed information the reader is referred to the Strategy and its appendices, which outline the entire waste management legal framework. Key legislation aimed at harmonizing Serbia with the EU in the areas of waste management and packaging waste were adopted on May 23, 2009; the adoption of these laws is driving the municipal waste management strategic planning process. The Law on Waste Management, in addition to other requirements, establishes a deadline for municipalities to complete both municipal and regional plans for waste management, and leading many municipalities to opt for international strategic waste management partners as previously discussed.
Note: This text is an excerpt from the document-guide for investors Secondary Materials and Waste Recycling Commercialization.
The project is implemented with the support of the USAID Serbian Competitiveness Project.

Companies:
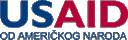

KALIMERO KOMERC KRUŠEVAC


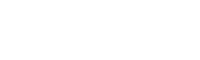



Tags:
Secondary Materials and Waste Recycling
Kalimero komerc
SFS
US Steel
BiS
IT recycling
Klaster galenit profil
Strugara Marinković
Grozd
Brest Parket
Dorado
construction waste
Stevanovic Invest
Lafarge
Šuša
Ecorec
Auto mirko
Bio King
Mikan Nešić
Composting Strategies for Serbia
Beacon Conference
Law on Packaging
Comments
Your comment
Most Important News
Full information is available only to commercial users-subscribers and it is necessary to log in.
Follow the news, tenders, grants, legal regulations and reports on our portal.
Registracija na eKapiji vam omogućava pristup potpunim informacijama i dnevnom biltenu
Naš dnevni ekonomski bilten će stizati na vašu mejl adresu krajem svakog radnog dana. Bilteni su personalizovani prema interesovanjima svakog korisnika zasebno,
uz konsultacije sa našim ekspertima.