(NOMINATION FOR 2016 AUREA AWARD): Euroheat - Production of Plate and Shell Heat Exchangers


September 2015 saw Kragujevac-based Euroheat launch the production of improved version of plate and shell heat exchangers, types P-500 and P-100, which are a hybrid of plate heat exchangers and shell heat exchangers, combining the best characteristics of each.
Unlike all the previous, these heat exchangers have no gaskets and internal plates are welded to each other instead, which makes them fit for operation in a wide temperature range and under high pressures. The efficiency level of plate and shell heat exchangers is very high, going up to 98%, and one of their greatest advantages lies in easy and fast cleaning.
The initial program to develop plate and shell heat exchangers was financed by the Innovation Fund with the EU funds, in cooperation with the World Bank, under the Innovation Support Project in Serbia. The company has also filed a patent.
All technical improvements have been achieved with reduced costs of production, that is, a lower product price, which additionally increases the market competitiveness of this product with improved technical characteristics.
This type of heat exchanger has found its application in almost all fields where there is a need for the exchange of heat between two fluids – in remote heating systems (very often used as primary heat exchangers with a capacity of few tens of megawatts), in cooling systems (as evaporators and condensers), and in the hydraulic oil heating and cooling industry.
The Euroheat company has already exported the first ten P-500 heat exchangers to Russia, while two P-1000 heat exchangers are sold to Majdanpek Heating Plant and one to Bor Heating Plant.
INNOVATION

Internal plates within innovated heat exchangers are welded to each other using machines that Euroheat workers designed themselves, so no gaskets are used, which allows this type of heat exchangers to operate in the temperature range from -200 to 500ºC as well as under extremely high pressures (up to 100 bar or even more). Besides, gaskets in old heat exchangers had a life of 5-6 years, after which they needed to be replaced, and cleaning was highly complicated. One of the greatest advantages of plate and shell heat exchangers lies in the fact that one side of the heat exchanger is easy and quick to clean (using just regular water under pressure), which is why this type of exchangers is very often used in large boiler plants as a primary heat exchanger, that is, as the boiler’s protection from dirt that could reach the hot water supply system.
Plate and shell heat exchangers are usually in use in thermal power stations and city heating plants which have so far been using mainly tube heat exchangers that take up a huge space. Although large, exchangers designed by Euroheat are smaller in size, occupying less space, while their efficiency is much higher than with tube heat exchangers, amounting to 98.4%.
All technical improvements have been achieved with reduced costs of production, that is, a lower product price, which additionally increases the market competitiveness of this product with improved technical characteristics.
Main advantages over similar products – technical improvements
- work with aggressive fluids – an expanded pool of aggressive working fluids in use
- work in a wider temperature range (from -200 do 500 ºC)
- improved transfer of heat between working fluids –an increased coefficient of energy utilization
- work under high pressures - efficient under a wider range of operating pressures than competitors
- simple structure – easy production, assembling, maintenance and handling
- possibility of adaptation for a large energy transfer capacity (100,000 kW)
- compact shape – easy to transport and assemble
- absence of gaskets –production is cheaper
- applicable in almost all industries
SOCIAL UTILITY

Development of plate and shell heat exchangers required a greater manpower, which is why the company hired 4 new workers in December 2015 alone (they now have 16 employees in total).
The entire production of plate and shell heat exchangers is carried out in Euroheat facilities in Kragujevac. When it comes to raw materials, they're using stainless steel sheet metal, and the main problem is the absence of a press in Serbia that can shape it in a quality manner, so this has had to be done in Italy to date. The company is now in talks with Chinese partners about the procurement of fully automated hydraulic press of 4,000 tonnes, which they say would be the only press of the kind in Serbia. Its commissioning will require the company to employ additional workers, so Euroheat announces new hires in 2016.
FINANCIAL POTENTIAL

Although the company is primarily engaged in the production of plate heat exchangers, they also make substations and calorimeters on order. In a very short time, the new plate and shell heat exchangers registered solid sales, so the company expects these models of heat exchangers to gain primacy in production in 2016.
Euroheat exported the first ten P-500 plate and shell heat exchangers to Russia in January. Russian partners visited the factory in Kragujevac to check the alignment of production process with Russian standards. The company possesses and applies ISO 9001, ISO 14001, ISO 18001, EAC (a standard for the Russian market, a replacement for GOST-R), while heat exchangers have been tested by the PED directive 97/23/EC as well.
Two P-1000 heat exchangers are sold to Majdanpek Heating Plant and one to Bor Heating Plant. The one in Bor is put into operation and works great. These heat exchangers in Bor and Majdanpek serve as primary heat exchangers (between the boiler and the hot water supply network). Heat exchangers are also set up in Kragujevac Clinical Center and the Meggle dairy.
Aside from Euroheat, there is also a company in Norway producing heat exchangers of this kind, but those made in Kragujevac are much cheaper although their quality is the same. Namely, despite the fact that they are more expensive than standard heat exchangers, plate and shell heat exchangers made in Kragujevac are about 40% cheaper than those produced abroad. Imported components (stainless steel sheet metal and steel plates) are the same as abroad, but the difference lies in the price of fuel and manpower as well as in the fact that Euroheat workers have innovated welding machines by themselves to make their job easier and cheaper.
Other comparative advantages over competitors
- rational and cheap production process – a reduced number of necessary workers and machines in production
- decreased fuel consumption and more rational use of raw materials – cheaper production in terms of primary material resources
- the company is the only manufacturer of heat exchangers of this kind in south Europe – a lack of competition in the regional market
- the company has already positioned in the markets of Western Europe, Russian Federation and Western Balkans – marketing campaigns make brand recognizable in crucial markets for the company
- the company possesses a sales and service network in ex-SSSR and ex-Yugoslavia countries – developed commercial activities in the markets where a new product is to be placed
- an agreement on tariff preferences between the Republic of Serbia and the Russian Federation, which additionally lowers the competitive price of the product and practically automatically eliminates competitors
- all existing products of the company are aligned with EU safety standards (CE-sign) and meet the requirements of the EAC standard (the Russian Federation) – a good rating of companny products in terms of fulfillment of basic preconditions for market penetration
- the company possesses certified management systems ISO 9001, ISO14001, ISO18001
If the production of plate and shell heat exchangers is your favorite for the Investment of the Year Award, you can vote for this nomination at the official website of the Aurea Award.


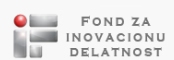
